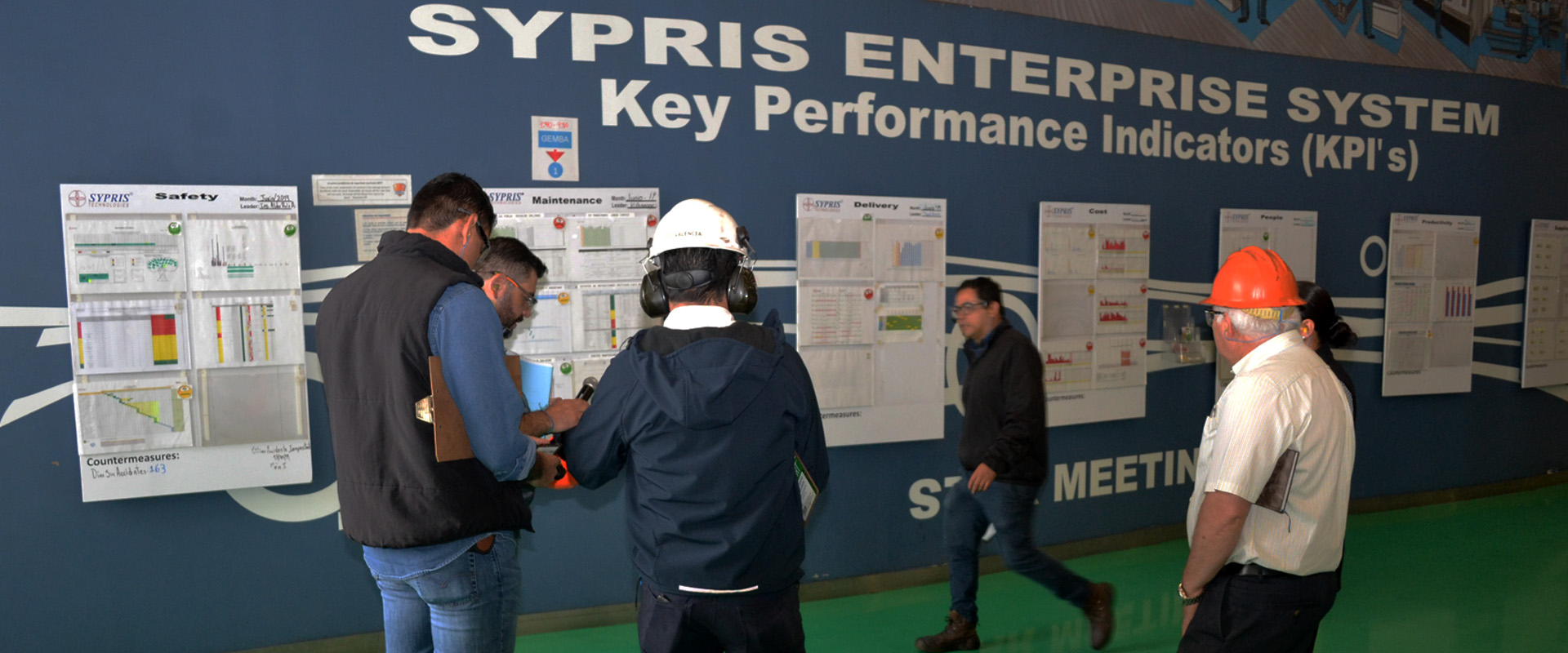
Continuous Improvement
Driving Excellence Through Systematic Process Enhancement
Culture of Excellence
Driving Improvement Through Innovation, Engagement, and Partnership
At Sypris Technologies, a commitment to excellence is deeply embedded in our company culture. We believe continuous improvement is not just a program, it's a mindset shared across all levels of the organization. We empower our teams to identify and act on opportunities for improvement, enhancing performance, efficiency, and product quality throughout our operations.
To further elevate our capabilities, Sypris has partnered with the Toyota Production System Support Center (TSSC) for over a decade, a respected not-for-profit organization affiliated with Toyota Motor North America. Through this partnership, we've adopted key elements of the Toyota Production System (TPS), including Just-in-Time production, Jidoka (built-in quality), and employee-driven problem solving.
Methodologies
The Sypris Enterprise System, grounded in lean manufacturing and operational excellence, forms the backbone of our improvement efforts.
We apply proven methodologies such as:
- Kaizen Events
- Value Stream Mapping
- 5S Workplace Organization
- Total Productive Maintenance (TPM)
- Quick Changeover (SMED)
With support from TSSC, we have further strengthened these efforts through direct coaching and guidance rooted in TPS principles, driving even greater process clarity, consistency, and efficiency.
Tools and Techniques
We use powerful tools to drive root cause resolution and sustainable improvements, including:
- Root Cause Analysis
- Statistical Process Control (SPC)
- Standard Work Development
- Visual Management Systems
- Team-Based Problem Solving
- Process Capability Studies
- Error-Proofing (Poka-Yoke)
Our collaboration with TSSC has enabled deeper integration of these tools into daily operations, reinforcing a culture of discipline and continuous learning.
Focus Areas
Our improvement initiatives focus on what matters most to our customers and stakeholders:
- Process Optimization
- Quality Enhancement
- Waste Reduction
- Cycle Time Improvement
- Cost Reduction
- Safety Improvement
- Environmental Sustainability
Implementation Strategy
Real transformation requires engaged teams. Through our partnership with TSSC, we've implemented a hands-on, team-based approach that empowers employees to take ownership of improvement activities.
We support this with:
- Cross-Functional Teams
- Performance Metrics Tracking
- Hoshin Kanri Process
- Best Practice Sharing
- Ongoing Training and Development
- Employee Recognition Programs
Key Benefits
- Enhanced Productivity
- Improved Quality
- Reduced Costs
- Faster Delivery
- Higher Employee Engagement
- Sustainable, Scalable Results

Related Capabilities
Automation
We continuously enhance our automation systems to improve efficiency and quality.
Learn MoreSypris Development Center
Our SDC drives innovative improvements in our manufacturing processes.
Learn MorePartner in Improvement
Our continuous improvement specialists can collaborate with your team to optimize processes and enhance quality in your supply chain.
Contact Our Team